INVENTORY FORECASTING FOR AEROSPACE
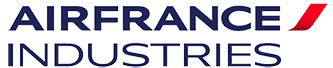
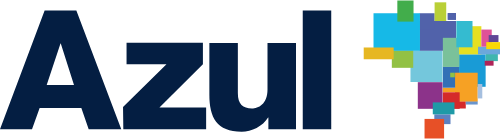
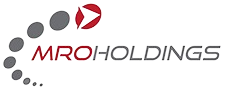
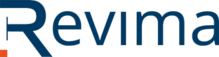
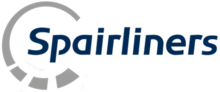
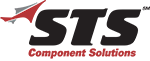

Aircrafts require a vast spectrum of parts to operate ranging from high-cost repairable parts to low-cost fast-moving consumables. Apart from the fact that certain parts are highly expensive, failure to have the necessary part readily available can also translate into expensive AOG (aircraft on ground) incidents. Lokad provides a statistical software solution that delivers in-depth inventory optimization through demand forecasting for airlines, MRO (maintenance, repair and overhaul) and OEM (original equipment manufacturers).
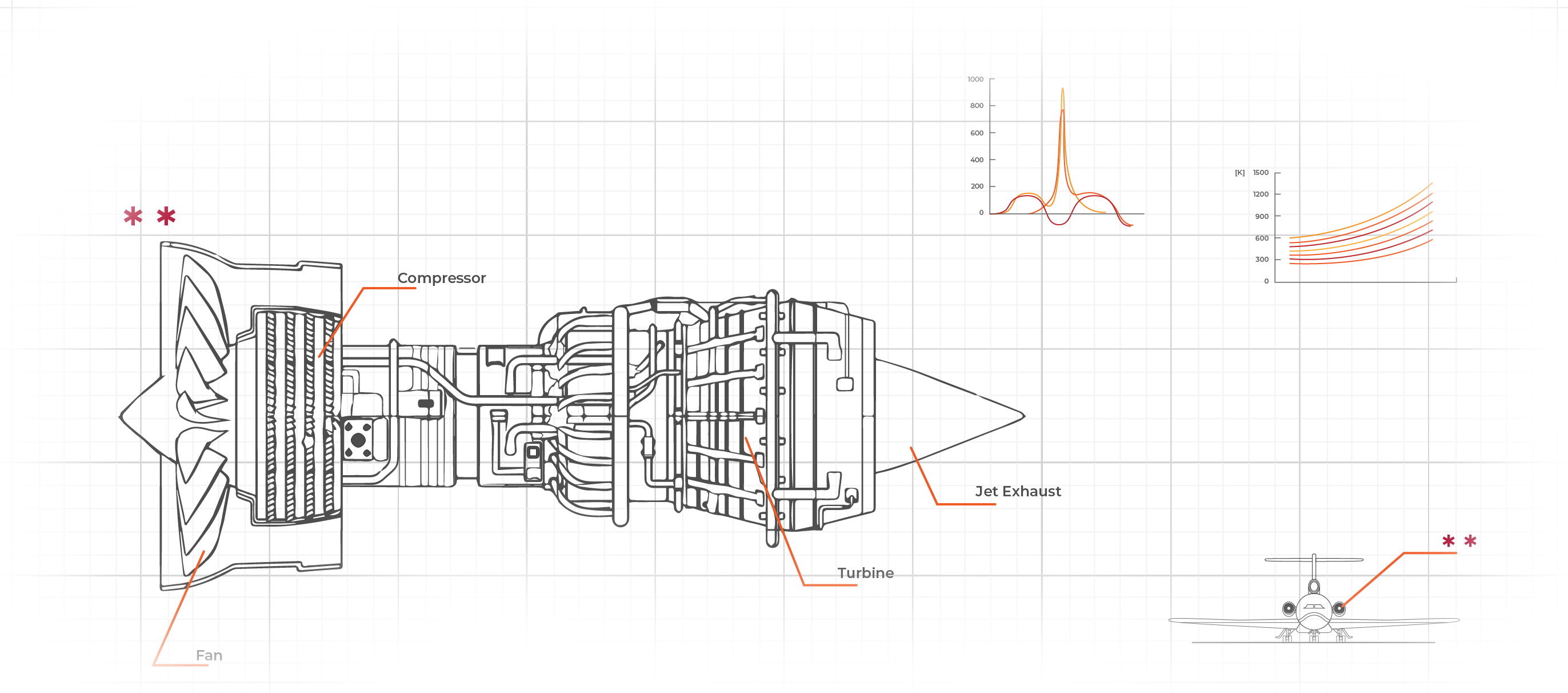
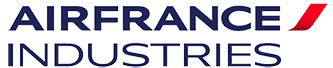
Air France Industries is the MRO arm of AIR FRANCE KLM with over 200 customers - international, regional, cargo airlines, etc.
Lokad brings a new tool to the table, one that is both powerful and innovative. But on top of that, Lokad has shared with Air France Industries its expertise in inventory optimization and Supply Chain management, thus bringing not only a complimentary IT solution but also a real consulting expertise, which our teams can rely on.
Charles Segondat, Head of Inventory Management, Air France Industries

"The entire Smart Planning project team at Airbus Atlantic is profoundly pleased with the successful completion of the initial phase of our advanced planning initiative. Thanks to the unwavering commitment, rigorous approach, and high-performing collaboration with the teams we have received the green light for the next steps and are excited and optimistic about continuing this journey together"
Julien Fournat
Project Manager Industrie 4.0 Airbus Atlantic
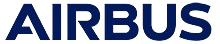
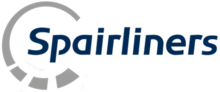
Spairliners is a global leader in spare parts equipment and maintenance for Airbus A380 and Embraer Ejet aircraft fleets.
We chose Lokad following an in-depth analysis of the inventory optimization solutions available on the market for our MRO activity (Maintenance Repair and Overhaul). Lokad's partnership-based approach and their reactivity, adaptability, and especially the performance of their solution led us to trust them with the inventory optimization of our aircraft spare parts equipment for our clients throughout the world. Lokad was successful in living up to the expectations and the complexity of our industry thanks to their original and intelligent approach to our needs.
Olivier Mazzucchelli, CEO of Spairliners, Hamburg, Germany

Video case study
LOKAD TV
Take a look at our interviews on Lokad TV and learn more about Supply Chain and aeronautics.
Classic approaches fall short for aerospace
As a rule of thumb, classic inventory optimization approaches perform poorly whenever spare parts are involved. In addition, the experience that Lokad has gained working in aerospace indicates that the situation is actually much worse in this specific industry.
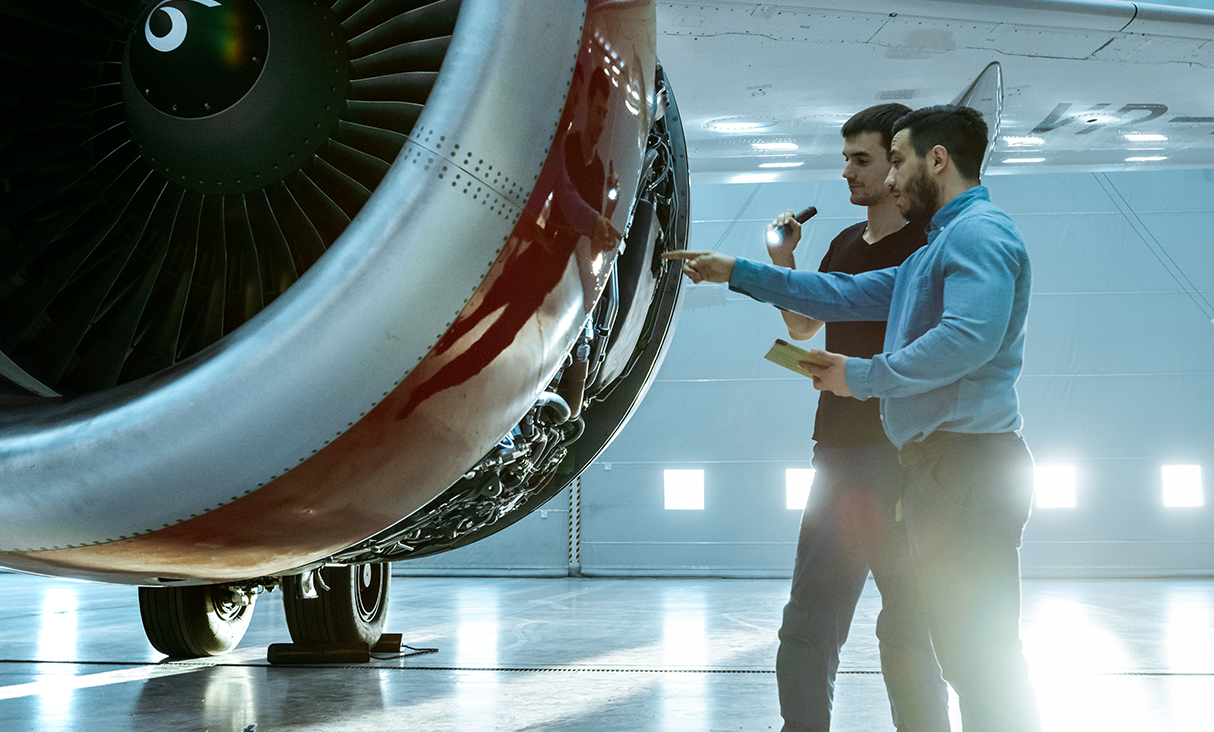
The high cost of certain parts, long lead times, infrequent failures and very steep costs of stock-outs only exacerbate all the weaknesses of classic inventory optimization.
In particular, time-series forecasts optimized against metrics such as MAD (mean absolute deviation) or MAPE (mean absolute percentage) do not properly reflect the highly asymmetric costs between overforecasting and underforecasting found in aerospace.
Classic safety stock analysis based on normal distributions or Poisson distributions also work poorly.
Classic safety stock analysis based on normal distributions or Poisson distributions also work poorly, because our data observations simply indicate that demand patterns do not actually follow either of these models. Similarly, ABC analysis fails because any classification that sorts all parts into a handful of inventory categories is unsuccessful in capturing the many different dimensions that define parts or consumables required by modern aircrafts.
Beyond the mismatch between the assumptions behind the classic models and the reality of the aerospace business, we have also found that classic approaches rely too heavily on a myriad of manual corrections. This frequently leads to situations where the manpower invested in inventory optimization is not capitalized, but merely consumed by IT systems just to keep up with daily operations. Some software design patterns, such as “alerts”, also tend to make the situation worse by focusing teams on daily superficial fixes, instead of focusing them on the root causes in order to deliver lasting solutions. For any inquiries, contact us at contact@lokad.com
Rethinking from scratch the mathematics needed by airlines to forecast their inventory.
Aerospace demand patterns require non-classic forecasts
Lokad’s analytical technology has been designed with aerospace drivers as its core. Instead of recycling forecasting and inventory models designed for other industries, Lokad created alternative statistical approaches where the specificities of the aerospace industry are natively built-in.
Lokad’s forecasting models reflect all these fleet-driven factors, not as mere corrective linear coefficients on top of time-series, but as the variables that fundamentally explain the demand itself.
Demand is first driven by the need to service an aircraft fleet. This fleet may grow or decline. The mix of flight hours and flight cycle also changes over time. Some maintenance operations are scheduled, others are unplanned. Lokad’s forecasting models reflect all these fleet-driven factors, not as mere corrective linear coefficients on top of time-series, but as the variables that fundamentally explain the demand itself. Also, it is not so much the “average” demand for parts that matters, but rather the spikes, i.e. the highest points of demand that impact service levels the most. Classic approaches that rely on normal distributions or Poisson distributions introduce systematic bias in all estimations.
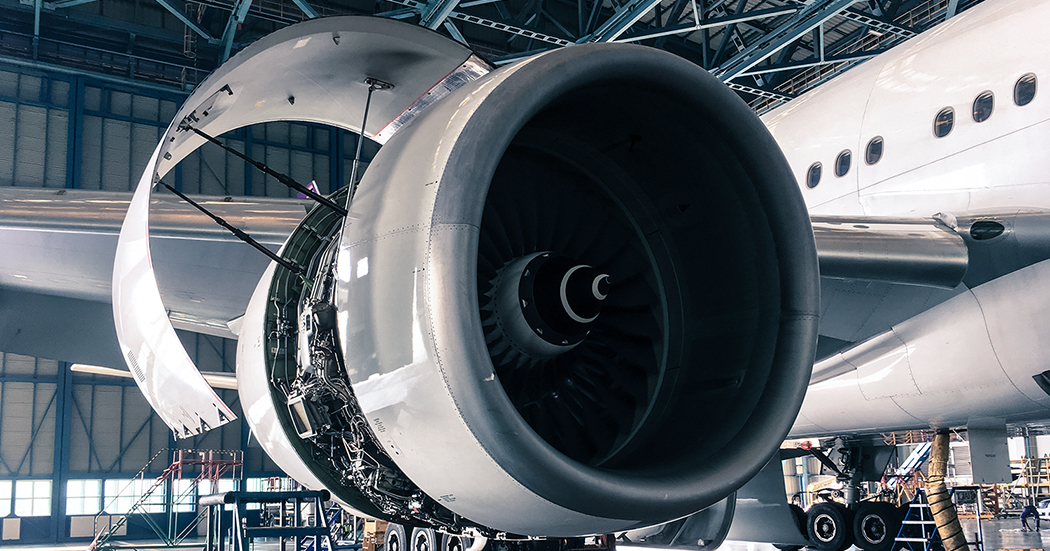
Lokad's technology relies on advanced quantile forecasting analysis of the demand. The quantile viewpoint is essential to accurately anticipate future spikes in demand and their corresponding probabilities.
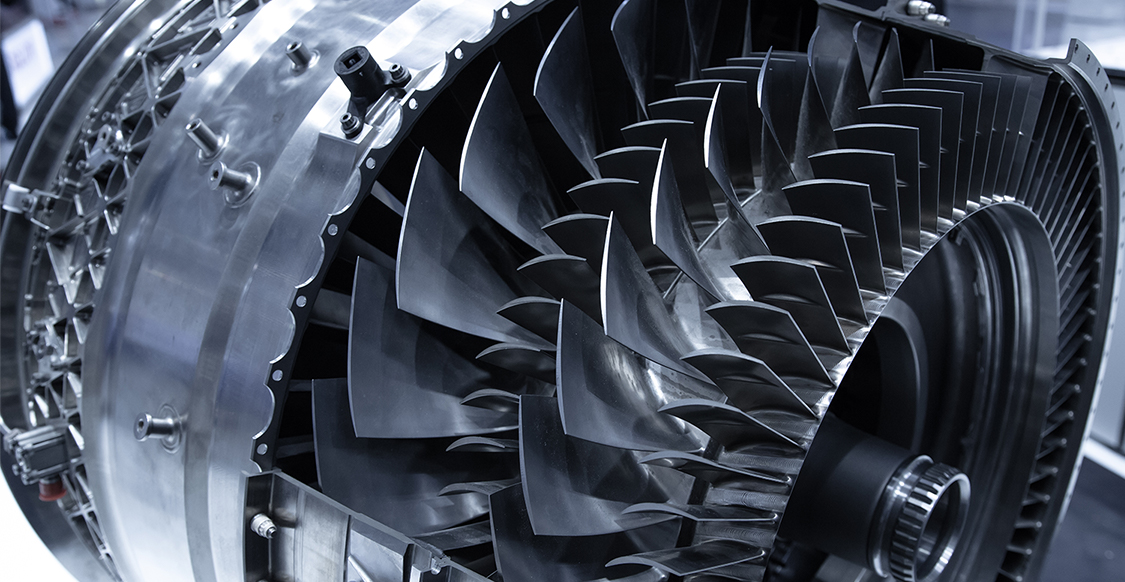
In addition, it is not only demand that is uncertain, but the lead times too. In particular, high-cost repairable parts involve not just one lead time, but an entire circuit, ranging from component change to renewed availability of the repaired part.
The complete lead time includes many steps: administrative time, procurement time, transit time, receiving time, TAT (inspection time at the MRO or OEM, and repair turnaround time if applicable), unloading and stock movement time, shop processing time, etc. Modeling an average or median lead time is vastly insufficient; Lokad’s technology directly models the whole distribution of delays - that is, the probability for any given delay to occur.
Finally, there are many highly specific patterns in the demand observed that require native statistical counterparts. For example, retrofits introduce multiple biases in the history that need to be accounted for. In addition, interchangeability rules concerning parts for which several versions coexist, fully interchangeable or just 1-way interchangeable, complicate the picture further. Unlike classic approaches which would try to cram everything into time-series, our technology addresses these issues in-depth via statistical models specifically tailored to these challenges.
Rethinking from scratch the user experience of the practitioners in charge of the inventory.
Inventory optimization aligned with aerospace costs
Parts must be serviced in order to avoid AOG (aircraft on ground) incidents, but in this respect, not all parts are equal. The concept of a part's essentiality with No-Go, Go-If and Go variants deeply impact the cost of not having the necessary part available.
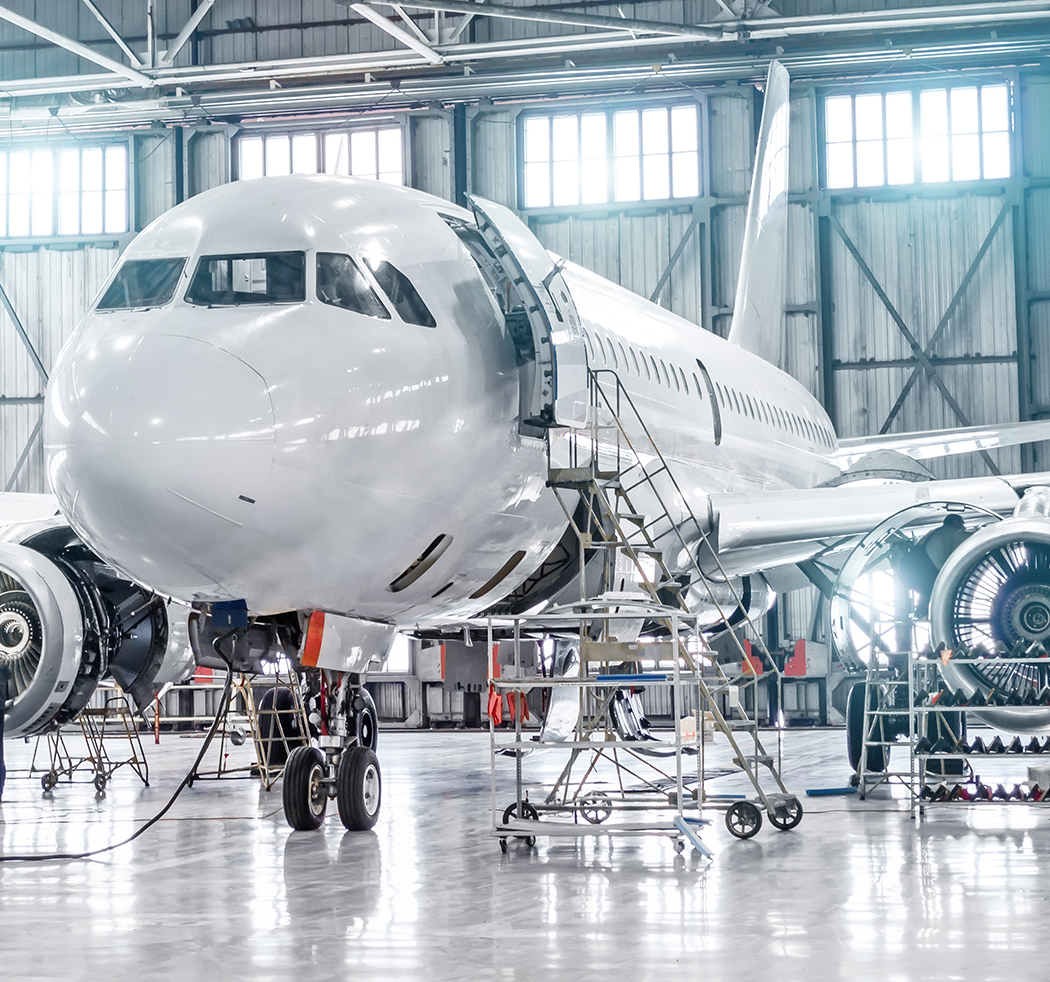
Many solutions incorrectly optimize a given forecasting error expressed in percents (ex: MAPE, the mean absolute percentage) or expressed with some other arbitrary unit (ex: MAD, mean absolute deviation).
In contrast, the core of our technology is designed to minimize the Dollars of forecasting errors. Our approach is very different from classic statistical systems that are simply “blind” to financial variables.
The costs involved with over-forecasts and under-forecasts are highly asymmetric in aerospace, and this has a deep impact on our technology. High-cost repairable parts are not only, as the name suggests, expensive, they also come with a “ratchet” effect on every purchase on the airline side. Indeed, as the scrap rate is very low for many parts, it means that any part purchased will remain as part of the inventory for years. And while reselling parts is sometimes possible, it frequently comes with a steep discount compared to the original price. Thus, our forecasts are natively and purposefully high biased to precisely reflect those asymmetric business situations. The goal is not to have the best inventory estimates in some abstract statistical sense, but the estimates that really help minimize business costs associated with the imprecisions of the estimates themselves.
In addition, while achieving better service levels is certainly a good thing if it does not involve holding more inventory, classic solutions target rather arbitrary service levels based on naïve inventory classifications frequently based on ABC analysis, or other similar variants. At its core, our statistical technology takes up the challenge of making the most of every single Dollar invested in inventory. For example, even if a part only has a 90% service level, while the company seeks a 98% service level overall, it might be more profitable to bring up the service level of another part from 98% to 99% if this part costs 100 times less and is requested 100 times more frequently than the former one. ABC analysis oversimplifies the aerospace inventory landscape where many different dimensions must be taken into account: unit cost, supply delay, essentiality, AOG purchase overhead, ATA chapter, potential obsolescence, etc.
Instead of delivering numbers that are “exactly incorrect”, Lokad strives to deliver numbers that are “approximately true”. Factoring in all the financial and operational constraints right into forecasting models proved to be a very challenging task, yet we have observed that relying on classic approaches that are “blind” to these factors gives very poor results.
Rethinking from scratch the relationship with the client to deliver the expected ROI.
Big Data approach for aerospace
Our technology is designed around the principle that we try to leverage as much data as possible as long as data is available, and naturally, as long as the data is actually relevant for any given inventory optimization challenge at hand. This viewpoint is different from the more classic approaches that have “hard” dependencies on specific data. If for some reason a certain amount of data is not available, there is simply no alternative in coping with this situation and ideally, the quality of forecasting should degrade as gracefully as possible when there is some data missing.
By utilizing more dimensions compared to classic inventory optimization models, Lokad delivers results that are more closely aligned to business-specific realities.
There is a mass of data that Lokad can leverage for inventory optimization. Among the most frequent items there’s the history of part purchases, part requests, component changes, repairs, scraps and part returns to name but a few.
Then the description of the fleet with its historical composition and all the relevant flight hours and flight cycles is also typically leveraged. Finally, data related to parts (or consumables) themselves with their properties such as essentiality, ATA chapter, criticality, bulkiness, dangerousness is also important for inventory optimization.
In addition, the costs of purchasing the parts, either in bulk at lower prices or facing an AOG problem at a much steeper price, also constitute some of the key ingredients in improving the “financial” accuracy of forecasting models.
Even something as seemingly simple as the state of inventory requires a relatively diverse set of data.Indeed, stock includes not only the stock on hand and the purchase order due, but also the future repair returns, serviceable part returns, loans to other airlines and parts lent to other airlines. By utilizing more dimensions compared to classic inventory optimization models, Lokad delivers results that are more closely aligned to business-specific reality.
Third-party data such as MTBUR values (mean time between unscheduled removal) as provided by OEMs can also be leveraged. However, instead of relying 100% on a single data source, our technology prefers to make the most of all the data available.
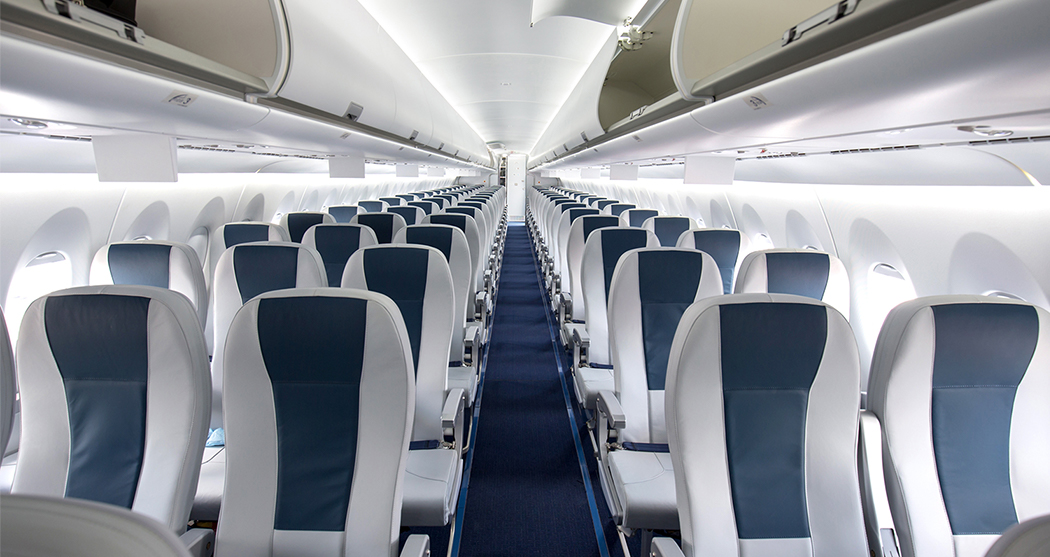
If a component has been changed more than 100 times, the estimated MTBUR based on historical data is almost certainly more accurate than the OEM estimate. But on the other hand, for a component that is changed very infrequently, the OEM estimate is the only relevant piece of information. Lokad's technology leverages the best mix of information necessary in order to minimize financial costs associated with uncertainty.
"Lokad has provided the right tools and support to improve our supply chain planning process and reduce the uncertainty by incorporating a probabilistic approach. Lokad has done an outstanding job helping us optimize our demand forecasting to achieve very demanding fill rate targets at diminished risk."
Rob Cords,
President at MRO Holdings
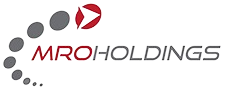