The Test of Supply Chain Performance
The ROI of a supply chain initiative depends on the performance of the software technology and on the skills of the people who execute the initiative itself. However, the ROI also strongly depends on the current supply chain performance, with lower performance offering more room for improvement. Below, we provide a simple test that can be carried out in minutes to assess your company’s current supply chain performance. Despite the simplicity of this test, we believe that it provides a more accurate perspective than most in-depth supply chain benchmarks and audits the market has to offer. It should take about 5 minutes of your time.
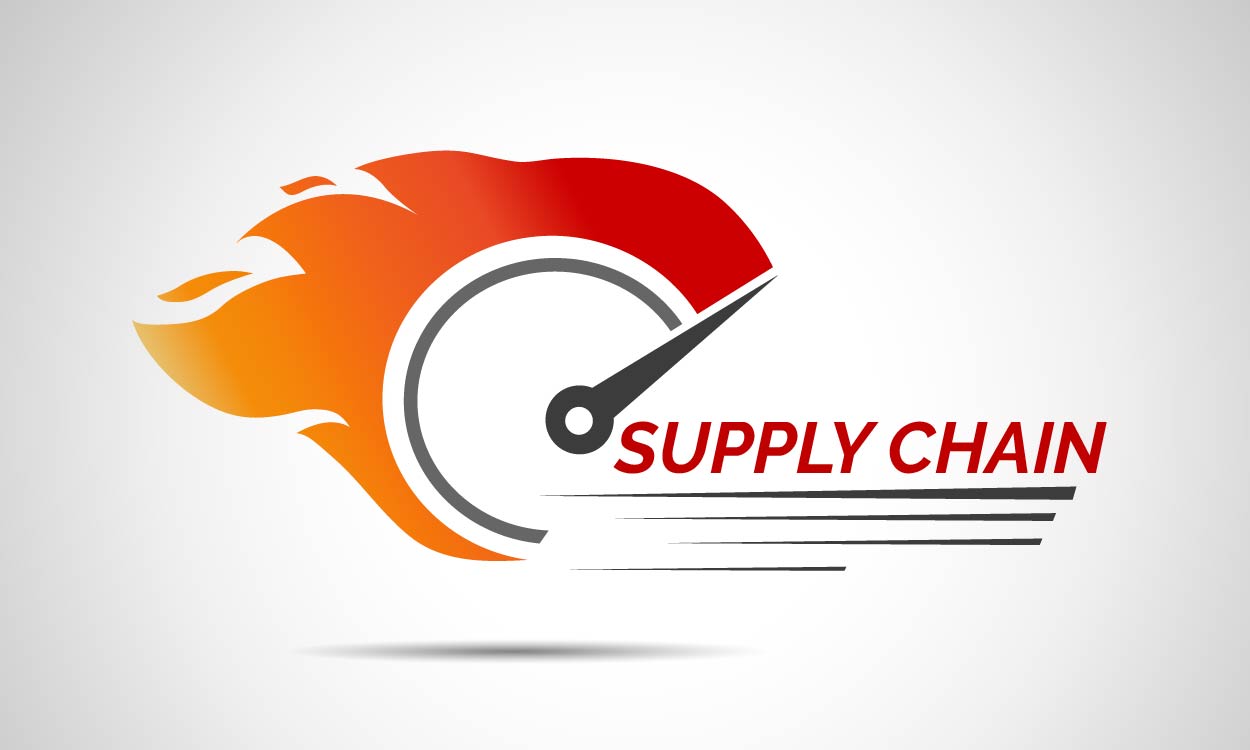
Your supply chain performance in 12 questions
- Can your supply chain operate without Excel?
- Do you consider ABC analysis to be obsolete?
- Is all relevant data documented by your supply chain teams?
- Do you record historical stock levels?
- Do your supply chain teams monitor the quality of their data?
- Do you forecast lead times?
- Do you prevent any manual intervention on forecasts?
- Do you manage operational constraints, - e.g. MOQs, - as data?
- Do you quantify the cost of supply chain failures?
- Can your decision-making systems be left unattended for a week?
- Can you recompute all decisions within one hour?
- Are all decisions prioritized against each other?
1. Can your supply chain operate without Excel?
If supply chain teams are using Excel sheets to generate their routine supply chain decisions - such as deciding on the quantities to be purchased - then operations can indeed be considered as being run through Excel. While using Excel once in a while for exploring data or for investigating a supply chain issue that had received little attention in the past is perfectly reasonable, keeping Excel in the loop of the daily decision-making process is not. Excel is not the right tool for generating thousands or even millions of decisions per day when a company wants to deliver a reliable supply chain process. If supply chain decisions depend on Excel, this implies in practice that those decisions are not nearly as optimized as they could be.
2. Do you consider ABC analysis to be obsolete?
ABC analysis boils down to classifying the thousands of products that your company is selling into 3 to 5 classes defined based on their recent sales volume. Yet, these ABC classes do not add any information. Instead, they merely reflect the historical demand - albeit in a crude manner - since most of the original information is lost. ABC analysis and all of its variants represent a weak method of analysis that attempts to mitigate the complexity of your supply chain through very rough approximations. If supply chain decisions rely on rules that involve ABC classes, then those decisions can be improved by simply removing the ABC classes and introducing more granular responses to projected future demand.
3. Is all relevant data documented by your supply chain teams?
The important part of this question is who gets to write the documentation. Frequently, there is little or no documentation available for supply chain data, which includes - among other things - sales history, purchase history, stock levels and product catalog. However, even when such documentation does exist, it may not have been written by the supply chain teams themselves, but rather by the IT teams. The documentation of the data needs to be written from a supply chain perspective, otherwise it is guaranteed to miss out on the many subtleties associated with the company’s supply chain processes. Lacking data documentation hinders many, if not most, of the attempts to fix long-lasting and ongoing supply chain glitches. In reality, those glitches are typically associated with the edge cases, which could have been properly handled by implementing precise rules dedicated to dealing with those specific cases. However, due to a lack of precise supply chain driven documentation, the company routinely fails at implementing those fixes.
4. Do you record historical stock levels?
You can’t optimize what you don’t measure; and the better the measurement, the easier the optimization. Supply chain requires keeping many historical datasets: sales history, purchase history, stock movement history, etc. However, too often, historical stock levels are not properly recorded. While ERP / MRP / WMS vendors might argue that this data would burden their systems, recording such data is hardly a challenge anymore thanks to the data storage capabilities that are available nowadays. Therefore, if your supply chain systems do not record your historical stock levels, then, most likely, there is very little in place to actually cope with the biases introduced by the stock levels themselves.
5. Do your supply chain teams monitor the quality of their data?
Again, the important part of this question is who does the monitoring. The quality of the supply chain data is a critical ingredient for keeping supply chain operations running smoothly. Yet, too frequently, supply chain teams have little or no means of monitoring the quality of their own data and acting upon it when the KPIs begin to deviate from their initial course. Value is in the eye of the beholder. The task of monitoring the quality of the supply chain data and proactively fixing issues that arise over time cannot be delegated to the IT teams. This should instead be one of the primary responsibilities of the supply chain. When the supply chain doesn’t embrace this responsibility, many glitches tend to remain unnoticed and invariably turn into costly - albeit usually dispersed - mistakes for the company.
6. Do you forecast lead times?
A good demand forecast is nothing without a good lead time forecast. In fact, in order to purchase or produce the right quantities at the right time, the company needs not only to correctly anticipate the future demand, but also correctly anticipate the timeframe to be covered. Lead times are varying, and just like demand, they exhibit many statistical patterns such as seasonality and uncertainty. For instance, the Chinese New Year increases lead times when manufacturing is carried out in China. When the lead times are not forecasted, the supply chain tends to react poorly to varying lead times since those variations are not planned for. The statistical forecast of the lead times addresses this challenge head-on, in order to make the most of the demand forecasts, which should be generated “on top” of the lead time forecasts.
7. Do you prevent any manual intervention on forecasts?
If a statistical forecast is incorrect, then the underlying statistical model should be fixed. If a statistical model is lacking some critical data that is otherwise available to the supply chain practitioner, then this data should be entered and made available to the system. If the statistical model cannot leverage this extra information, then this model should be changed in favor of a better one that can account for this additional information. There is no good reason for tolerating manual interventions on forecasts, or even on forecast models: not only are they a major waste of time, but they also distract supply chain practitioners away from the resolution of the underlying problems that generate the need for manual interventions in the first place.
8. Do you manage operational constraints, - e.g. MOQs, - as data?
Beyond transactional data such as the sales history, many other data sets are important for making supply chain decisions: MOQs (minimum order quantities), transportation costs, maximum container volumes, supplier price breaks, commercial quotas, contractual penalties, etc. Given that routine supply chain operations are dependent on this data, it should be treated as production data. However, too often, most of the above-mentioned data is not even properly tracked within the production IT systems. Instead, this data is usually kept in Excel sheets or Access databases which remain mostly unknown to the IT department. Not having all this data as part of the core IT systems typically indicates that production relies on unreliable data sources, such as the very same Excel sheets or Access databases. Consequently, the supply chain is not fully optimized to be able to cope with the type of constraints mentioned above, in the most efficient way.
9. Do you quantify the cost of supply chain failures?
Supply chains routinely fail to deliver: stock-outs happen all the time, dead inventory happens all the time too. While there is no question that reducing the frequency and the magnitude of such failures is not only desirable but nearly always possible, perfection is not a reasonable goal. A certain degree of supply chain failures will always take place because seeking perfection - i.e. zero failure - would be tremendously more costly than the failures themselves. There is a balance to be found between the cost of stock and the cost of stock-out. If the economic costs associated with supply chain failures are not quantified, there is no way of knowing whether the company is actually taking too little or too much risk. In practice, this implies that the company is not properly optimizing the risks relating to its supply chain.
10. Can your decision-making systems be left unattended for a week?
Millions of decisions need to be made each week when it comes to any sizeable supply chain. While the IT systems might be supported by the supply chain teams, the latter cannot reasonably micro-manage every single decision - there are simply too many of them. As a result, all modern supply chains operate by using at least some degree of automation, possibly via concepts as crude as Min/Max inventory. If the supply chain decision-making systems cannot be left unattended for a week, it means that those systems undoubtedly produce inadvisable decisions bound to hurt your company. In practice, it also implies that these “inadvisable” decisions are made constantly, simply because there is often no one available to manually override such decisions. Thus, if your company doesn’t trust its own automation to keep things running smoothly for a week, there is much to be gained from fixing the “inadvisable” parts of the supply chain automation.
11. Can you recompute all decisions within one hour?
Agility is essential in any supply chain. Business contexts change and what-if scenarios need to be investigated all the time. There is frequently no point in having a real-time response from the systems when it comes to changing a core hypothesis, such as transporting goods by air or by sea. However, when it comes to the supply chain models, it is critical that a response can be obtained within an hour or so. Supply chain management should be able to get feedback within the same day about an approach they would like to test, at the very least from a simulation perspective. Since simulations typically require a couple of attempts to “get it right” with the proper settings - unless all the models can be re-executed within one hour - there is no chance of getting such feedback within the day. Companies that don’t have the capacity to regenerate all supply chain decisions with varying hypotheses are companies that cannot explore the supply chain options that are available to them either. A lot of potential is thus left untapped.
12. Are all decisions prioritized against each other?
Many traditional supply chain systems place a strong emphasis on silos: decisions are made locally without considering the bigger picture. For example, if a warehouse is running low on a specific product, it is best to make sure that the few units of stock that remain are distributed to the stores that need them the most. When decisions are taken in isolation, a single store might place a big reorder for the product and thus generate a stock-out in the warehouse, while the store didn’t really need to reorder that much at this specific point in time. Companies that make their supply chain decisions in isolation are systematically missing the bigger picture by forgetting that most supply chain decisions tend to have non-local consequences. Therefore, unless your supply chain decisions are already systematically prioritized against each other, there are performance gains that lie in setting up such prioritization.